Case Study - Mayer Recycling
- Melanie Wraniek
- Jul 7
- 4 min read
From brand to industry solution
Mayer Recycling GmbH, based in St. Michael (Styria), is an established specialist in the processing and recycling of industrial and commercial waste. The company supplies thermal utilisation plants and industrial partners with quality-tested substitute fuels from its state-of-the-art plant park.
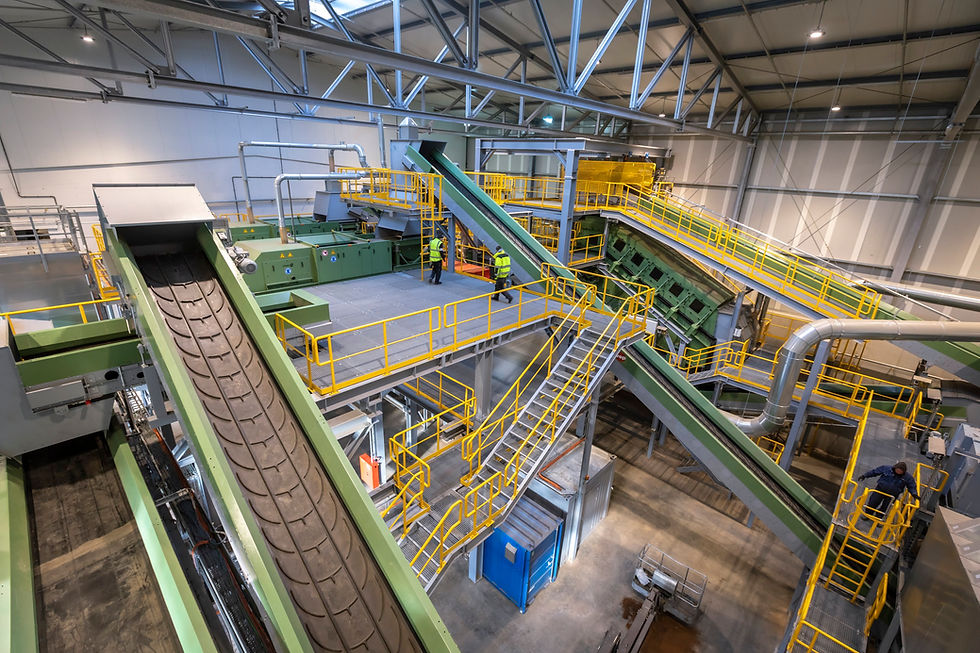
The 2018 fire and the search for safety
In 2018, the company was shaken by a serious fire. Within a few minutes, the material in a central bunker ignited - with far-reaching consequences for buildings, machines and ongoing operations. The cause: a combination of invisible heat development, often undetected batteries and highly flammable materials that are potential causes of fire due to friction or their material properties. Furthermore, stringent regulations and insurance requirements made it difficult to quickly get back to day-to-day business. Immense investments in conventional fire protection tied up capital and were only effective when it was usually already too late. A quick, easy-to-install solution had to be found that was inexpensive to implement, smart and reliable. A solution that nips major damage in the bud and prevents downtime and high downtime costs. In addition, there was the emotional component, the uncertainty of what would happen next and the concern of the employees and their families. As an entrepreneur with a heart, something had to be done to make such incidents a thing of the past. As a result, an intensive but fruitless search began for a suitable protection or early warning system that was adapted to the special conditions of the recycling industry. Numerous providers were contacted - none were able to deliver an integrated, robust and real-time-capable solution that met the industry's requirements.
As a result, an intensive but fruitless search began for a suitable protection or early warning system that was customised to the specific conditions of the recycling industry. Numerous suppliers were contacted - none were able to provide an integrated, robust and real-time capable solution that met the industrial requirements. Detection systems of various types were evaluated, but the trade-off between effectiveness, material loss and reliability was too great to be economically viable.
Fire 2018 at Mayer Recycling
The foundation of SAMsoric
Andreas Säumel (Managing Director at Mayer Recycling) and Dr Michael Autischer (expert in imaging processes) founded SAMsoric GmbH in 2019 in response to this need.
Declared goal:

The development of an industry-optimised machine protection system that is specially designed for recycling plants, according to the guiding principle: Developed by practitioners - for operators of recycling plants of the future The practice-oriented approach was at the centre of product development. SAMsoric was not designed as a theoretical concept, but was tested, validated and further developed directly in live operation at Mayer Recycling.
Solution approach and system integration
Volume flow measurement with SAMsoric VOLPower
A key element of the protection concept was the introduction of a high-precision volumetric flow measurement system that continuously records material cross-sections on the conveyor lines.
3D measurement using imaging techniques
Real-time data acquisition
Feedback to the system control for automatic adjustments
Volume-based material tracking through to final disposal
The resulting benefits:
Precise knowledge of the volume flow now enables optimally controlled material distribution, prevents overfilling and significantly increases throughput - while at the same time reducing susceptibility to faults.

Fire prevention with SAMsoric HSD sensors
The HSD sensors (Heat Source Detection) developed by SAMsoric form the centrepiece of the fire protection strategy. In contrast to conventional thermal sensors, the HSD modules analyse the heat source:
Localised temperature rises
Irregular heat sources (batteries, metals, chemical reactions)
Automated response:
As soon as a critical development is detected, automated measures take effect:
Stopping the conveyor belt
Isolation of the danger zone
Activation of extinguishing or cooling processes
Logging and alerting of operating personnel

Many years of testing and perfecting:
All SAMsoric products were tested over several years directly at Mayer Recycling in live operation - in real time, under full load and under real fault conditions. feedback loops between plant operation and the development team enabled targeted further development - with a focus on robustness, low maintenance and industrial compatibility.
Results and benefits | Before integration (2018) | After integration (from 2022) |
---|---|---|
Fire-related downtime | 1 major fire, 2 incidents/year | 0 incidents (since 3 years) |
Throughput capacity | approx. 12 t/h | > 16 t/h (+33 %) |
Material losses and disruptions to system operation due to overflow | regularly | almost excluded |
Maintenance time due to faults | > 20 h/month | < 6 h/month |
Conclusion
The integration of SAMsoric machine protection systems at Mayer Recycling is more than just an implementation project - it is the birth story of a new technological solution that arose directly from the needs of the industry. What began as a response to a fire that threatened the company's existence developed into a protection system that now sets standards throughout the industry. SAMsoric thus exemplifies the guiding principle
guiding principle: ‘Developed by practitioners - for operators of recycling plants of the future.’
Comments