Case Study - ThermoTeam
- Melanie Wraniek
- Jul 7
- 3 min read
ThermoTeam is a leading supplier of refuse-derived fuels (RDF) based in Retznei, Austria. The company is part of a joint venture between Lafarge ZementwerkeGmbH (Holcim Group) and Saubermacher Dienstleistungs AG.
ThermoTeam processes over 100,000 tonnes of processed waste every year and supplies substitute fuels for co-incineration in the neighbouring LaFarge cement plant. The aim is to reduce fossil fuels while at the same time utilising industrial and commercial waste to generate energy.
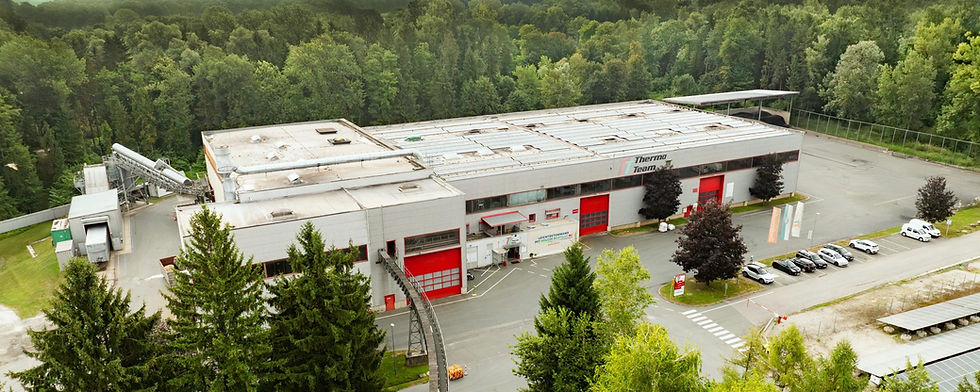
Initial situation and challenges
With increasing demands on efficiency, safety and sustainability, ThermoTeam and its partners Lafarge/Holcim faced several challenges in the recycling process:
Unclear volume flows along the conveyor lines made precise system control difficult
Belt scales are rather inaccurate in certain applications and require constant attention from the operator
Volume figures often reflect actual utilisation better than tonnes/hour
Increasing fire risks, especially due to batteries and reactive substances in heterogeneous input material
Desire for higher throughput without jeopardising operational safety
Minimisation of unplanned downtime, particularly with regard to security of supply for Lafarge
Integration of SAMsoric machine protection systems
To solve these challenges, ThermoTeam worked closely with SAMsoric to implement a comprehensive system concept for real-time monitoring and process reliability of material flows. The central components:
The key components:
Volumetric flow measurement with SAMsoric VOLPower
with SAMsoric VOLPowera. Using innovative 3D imaging and sensor fusion technology, SAMsoric continuously measures the material cross-section and volume flow on all conveyor lines. This data enables:

real-time optimisation of the material flow
Precise batch tracing
Avoidance of overload or underload in the system at relevant machines and system components. This resulted in better utilisation of the system technology and a significant increase in throughput.
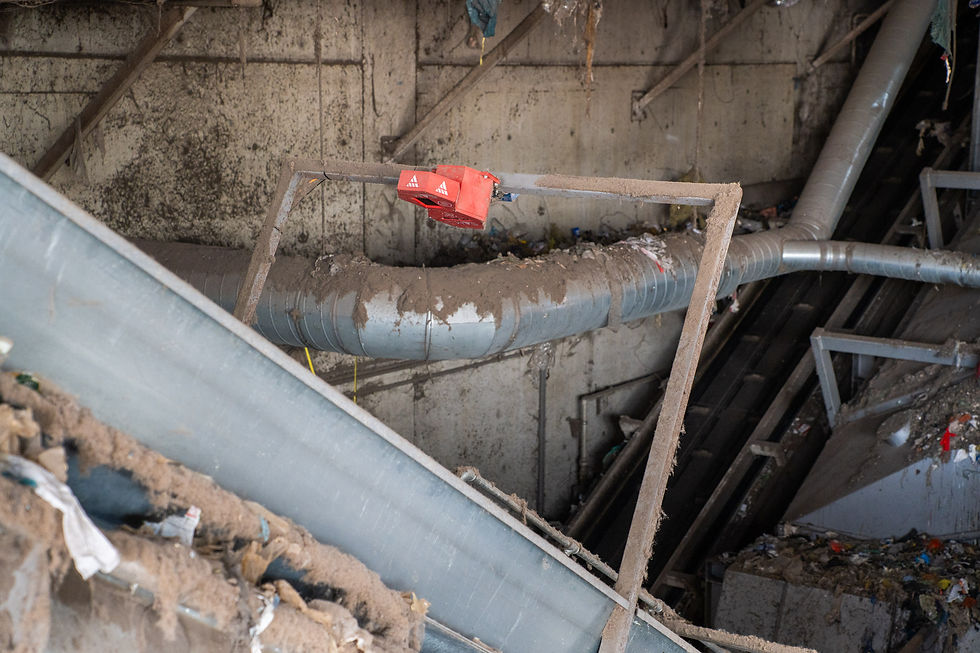
Fire prevention with SAMsoric HSD sensors
To detect potential sources of fire, SAMsoric HSD (Heat, Smoke & Detection) sensors were installed at key points in the process - particularly in transfer areas, bunkers and before and/or after the shredders.
The sensors detect:
Local temperature rises.
Smouldering processes
Conspicuous thermal objects (e.g. batteries)
If an alarm is signalled, the conveyor unit is automatically stopped, the affected segment is isolated and, if necessary, an extinguishing or cooling system is activated.

Intelligent system integration with Lafarge/Holcim
A central element of the solution was the seamless connection to the Lafarge/Holcim ERP and process control system. This means that safety-relevant information from the ThermoTeam plant is integrated directly into the cement line's supply process:
Automatic stops in the event of temperature or volume anomalies
Data transfer for performance analysis
Early warning messages in the event of irregularities in the input
Results and benefits
Results and benefits - Key figures | Before | After the integration of SAMsoric VOLPower |
---|---|---|
Throughput performance | approx. 18-20 t/h | über 24 t/h (+20–25 %) über 24 t/h (+20–25 %) |
Fire-related shutdowns | 2–3 Zwischenfälle/Jahr | |
Material feed / optimisation of throughput and system utilisation | ±15 % | < ±3 % (thanks to volume flow data) |
Recognised heat sources with potential fire hazard | A few | Early detection in any case |
Conclusion
The integration of SAMsoric machine protection systems at ThermoTeam is an example of how modern sensor technology can significantly increase both safety and efficiency in industrial waste utilisation. The combination of precise volume flow measurement and early thermal hazard detection not only enables higher throughput, but also seamless, trouble-free supply to critical industrial partners such as Lafarge/Holcim.
ThermoTeam is thus positioning itself as a technology leader in the field of safe, predictable substitute fuel production of the future.
Comments