Case Study - TriPlast
- Melanie Wraniek
- Jul 7
- 3 min read
Triplast GmbH is a leading plastics processing and recycling company based in Enns, Upper Austria. As part of the new construction of what is currently Austria's largest plastics sorting plant, Triplast was looking for innovative solutions to safeguard its machines and systems, particularly with regard to the increasing risks of lithium-ion batteries igniting in the recyclable material streams.

Challenge
The increasing proportion of old electronic devices in plastic recycling harbours considerable risks due to incorrectly disposed lithium-ion batteries. These are one of the most common causes of fires in sorting and shredding plants. Triplast was faced with the challenge of reliably protecting both its employees and its plants from thermal incidents and explosions without compromising process efficiency.
Warehouse management
SAMsoric also offers a reliable solution for monitoring open-air warehouses, boxes and bunkers. A high-resolution outdoor camera reliably monitors storage areas outdoors or in warehouses. Fires occurring in outdoor areas can be reliably detected and appropriate measures can be taken immediately. On the one hand, this prevents a fire from spreading and, on the other, offers 24/7 monitoring of large areas without the need for personnel and without endangering life and limb.
Integration of SAMsoric systems
To fulfil the requirements, Triplast relied on the technologies of SAMsoric, a specialist in intelligent machine protection systems. Together with the manufacturer, a customised safety concept was developed that integrates several core technologies:
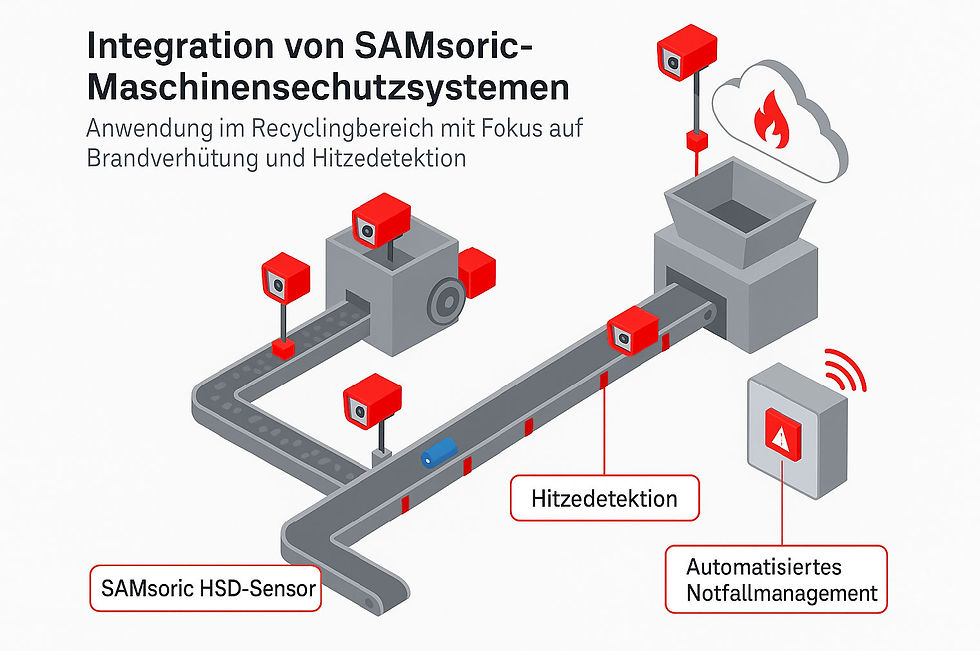
Thermographic early detection systems
Thermal imaging cameras from SAMsoric were installed at critical points in the sorting plant. These continuously monitor the temperature development in conveyor areas, bunkers and in front of the shredder. Potential sources of fire - in particular due to damaged or overheated batteries - are thus recognised at a very early stage. If detected, a cooling section is triggered and, if necessary, the spread of heat sources is prevented by switching off the relevant area.
Object detection and battery detection
A central element of the system is the automatic detection of fire hazards using AI-supported multi-sensor systems. By combining optical, thermal and spectroscopic data, batteries and objects with high, sometimes critical temperatures can be identified in real time and specifically cooled, extinguished or ejected.
Automated emergency management
Automated processes take effect in the event of a hazard report: Conveyor systems are stopped, affected areas are encapsulated and cooling or extinguishing processes are triggered. This is done in coordination with an intelligent control system, which also informs or alerts the plant management and other relevant authorities. All events are documented with a video stream and can be evaluated for subsequent analysis by the authorities, insurance companies or the fire brigade.
Results and benefits
Since commissioning the SAMsoric system, Triplast has been able to recognise potential hazards in advance and nip drastic consequences for people and the environment in the bud.
Furthermore, significant improvements in operational safety and risk prevention have been recorded:
Almost no fire incidents since the introduction of the system despite higher throughput volumes
Reduction in downtimes through proactive fault prevention; downtimes can be significantly reduced through measures adapted to the situation. This drastically increases overall plant availability
Increased employee and plant safety: risk to life and limb significantly reduced by monitoring critical parts of the plant
Summary
The successful integration of SAMsoric protection systems at Triplast demonstrates the potential of modern sensor technologies in industrial recycling. Particularly in a safety-critical environment such as battery recovery, they make a significant contribution to the prevention of serious operational disruptions and the sustainable safeguarding of production processes. Triplast is now regarded as a best-practice example of the use of intelligent fire prevention and detection solutions in plastics recycling.
Comments